Innovative GPS Sleeper Layer System Using Augmented Reality Software Revolutionising Rail Maintenance
Location
PilbaraThe Challenge: Re-Thinking Traditional Rail Sleeper Laying Techniques To Improve Safety And Efficiency
For many years, the rail industry had relied on traditional practices for laying sleepers, which proved to be labour-intensive and laden with risk. The process usually required a team of 6-10 workers involved in manual adjustment and measuring of sleeper positions, putting them potential ‘danger zones’ close to operating plant.
Not only posing the risk of being struck by plant – as well as manual handling and repetitive strain injuries – this process also contradicted ‘human vs machine’ exclusion zones set by mining companies in the Pilbara.
The Solution: Machine Guided Sleeper Laying System Removing Personnel From the Line of Fire
In response to these challenges, PRM collaborated with operators, supervisors and engineers to design a revolutionary GPS-guided sleeper laying system. The innovative system combines a custom-engineered sleep lug attachment with a hi-rail excavator and machine-controlled guidance system.
This advancement enables a single operator to lift and place steel sleepers directly from the track, eliminating the need for rail surveyors and multiple ground-based technicians.
By integrating augmented reality (AR) software, operators can view design models and their surroundings in real-time, significantly reducing the risk of injury and error. The system automates sleeper alignment and positioning, eliminating the need for constant measuring and adjustment by ground workers.
The Outcome: Eliminating Safety Risks and Improving Quality
The implementation of this innovative system has led to a significant enhancement in safety standards by:
- Eliminating the risk of people/plant interface with moving machinery.
- Reducing pinch/crush hazards for employees handling sleepers.
- Eliminating the need for workers to manually straighten sleepers using crowbars, reducing manual handling risks.
The system has also improved the quality of sleeper laying, ensuring greater accuracy in the process. It also allows for quick alteration of sleeper spacing specifications without the need for rework.
Compliance with required exclusion zones is ensured, as no other workers need to be involved in the task.
The successful integration of AR software technology with machinery in this innovation has the potential to revolutionise the rail industry’s sleeper laying process, setting a new standard for safety and efficiency.
PRM’s GPS Sleeper Layer System has been successfully implemented on the Rio Tinto track renewal project and has garnered national recognition at the National Rail Industry Awards and Rio Tinto Supplier Recognition Awards.
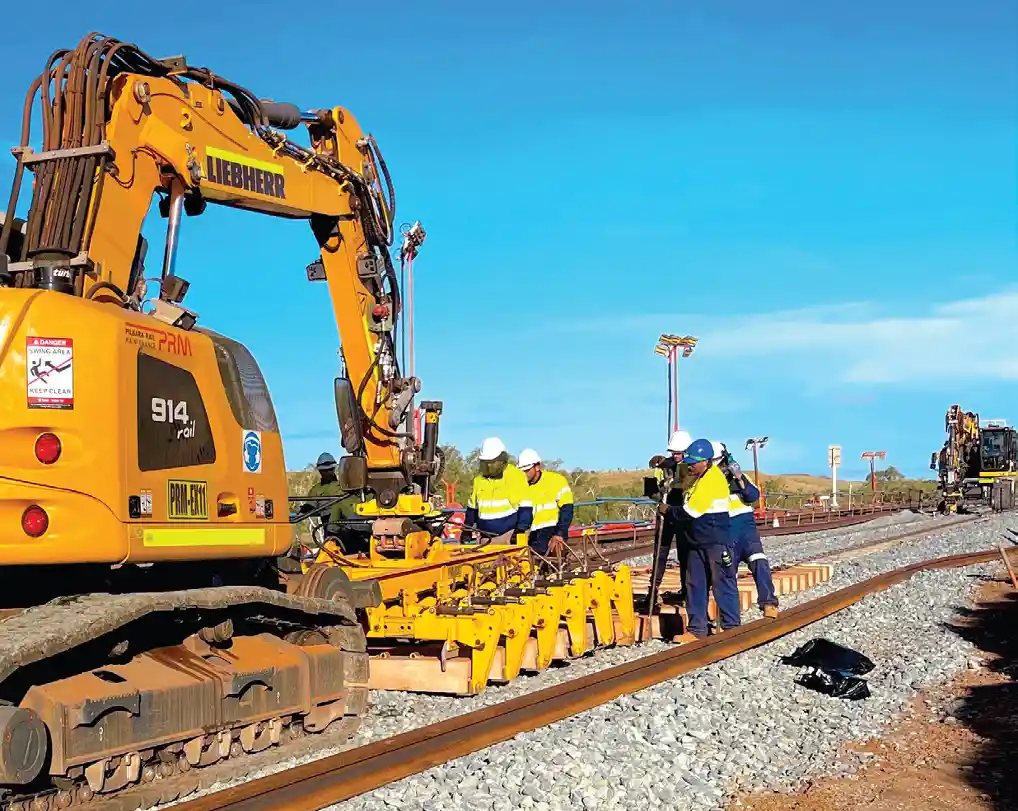
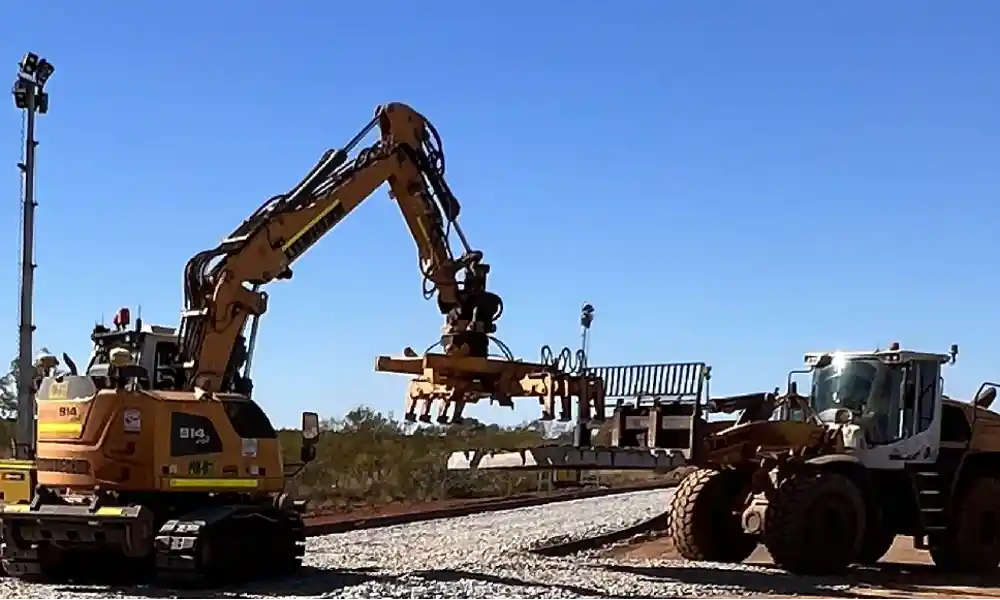
explore case studies
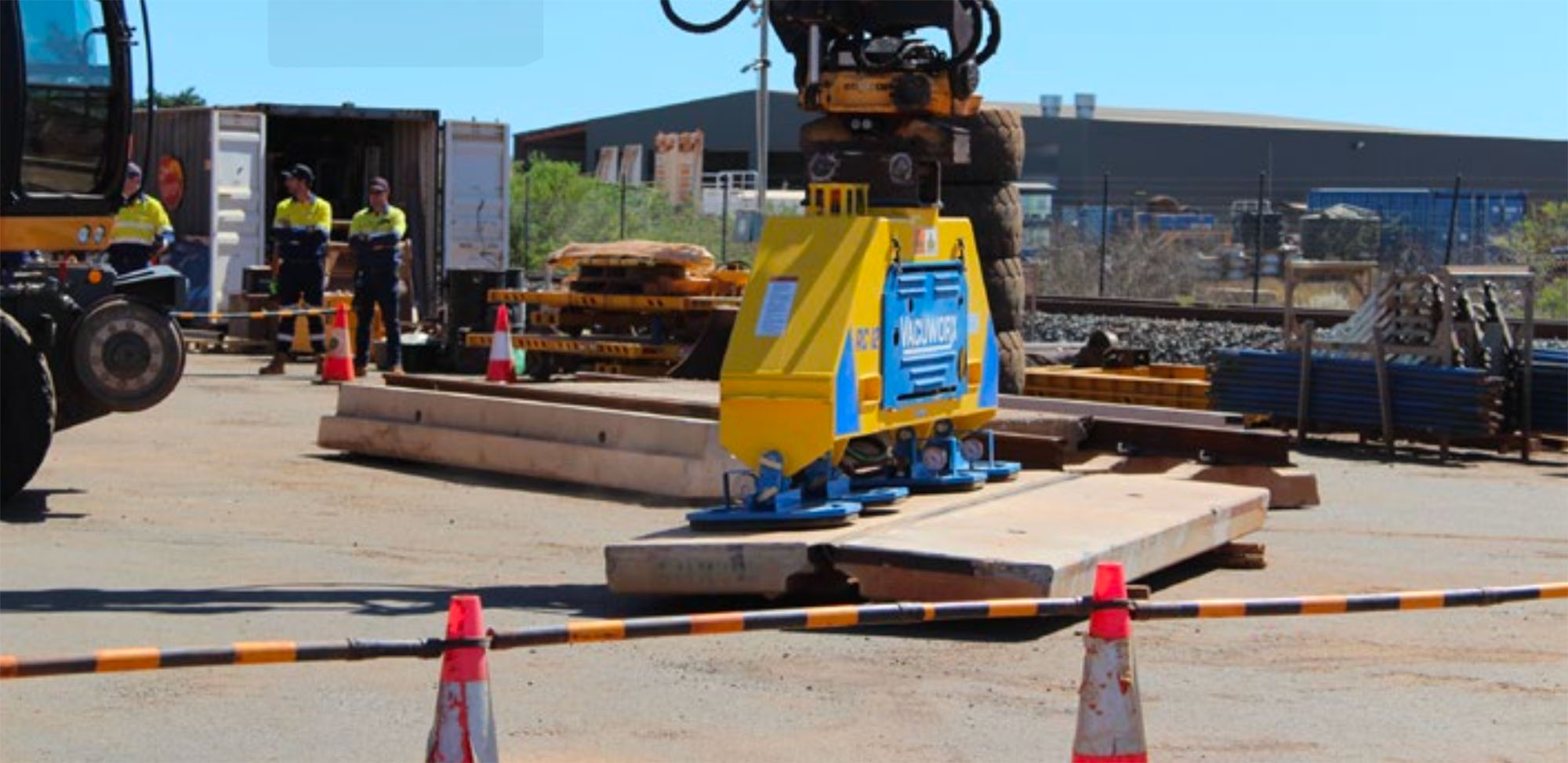
Vacuum Panel Lifter System Boosting Safety and Productivity
Seeking a more efficient solution for panel lifting, PRM invested in a VacuWorx vacuum system and customised it for rail works in an industry first.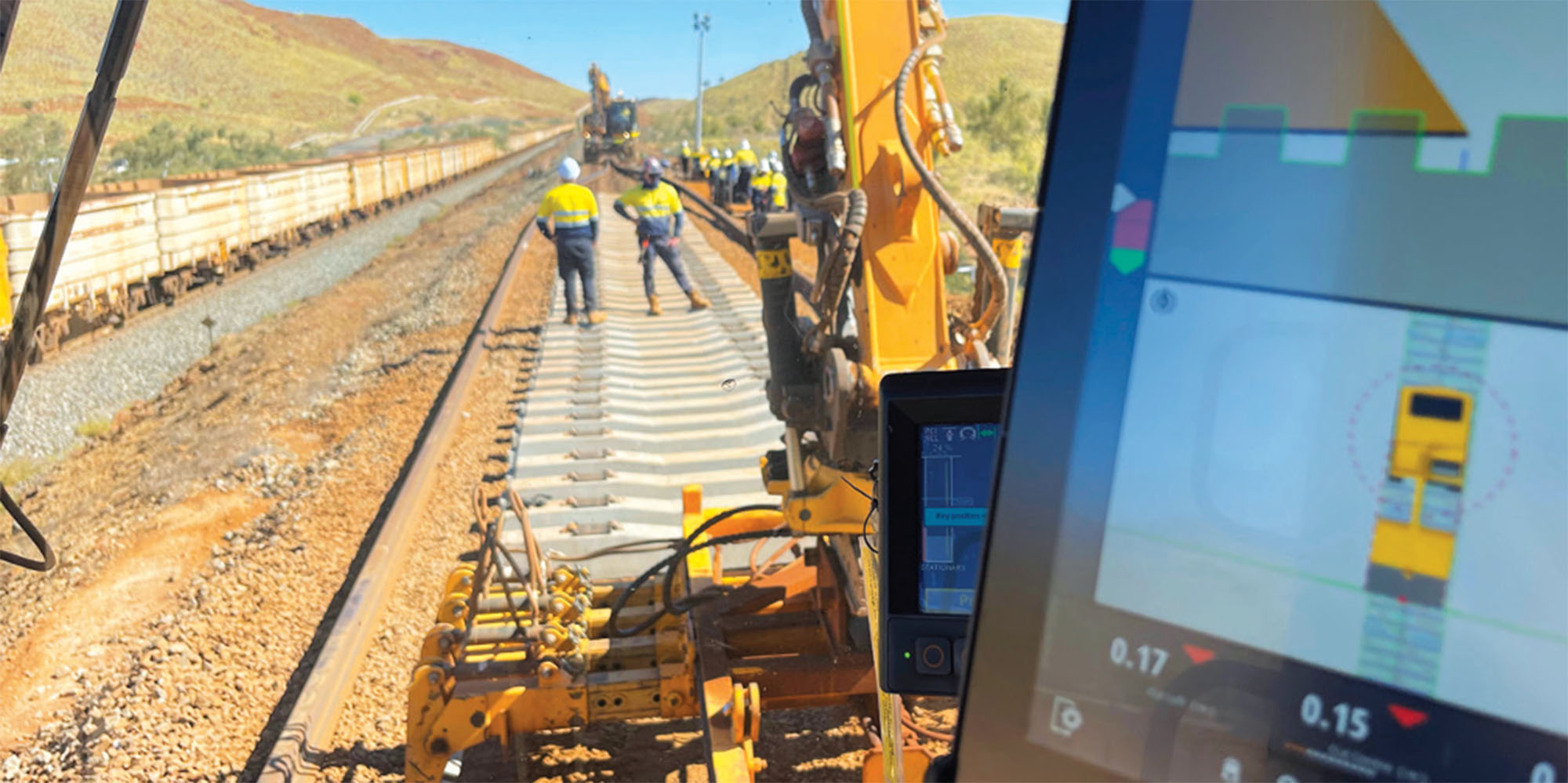
Innovative GPS Sleeper Layer System Using Augmented Reality Software Revolutionising Rail Maintenance
In response to the challenges present in traditional rail sleeper laying techniques, PRM collaborated with operators, supervisors and engineers to design a revolutionary GPS-guided sleeper...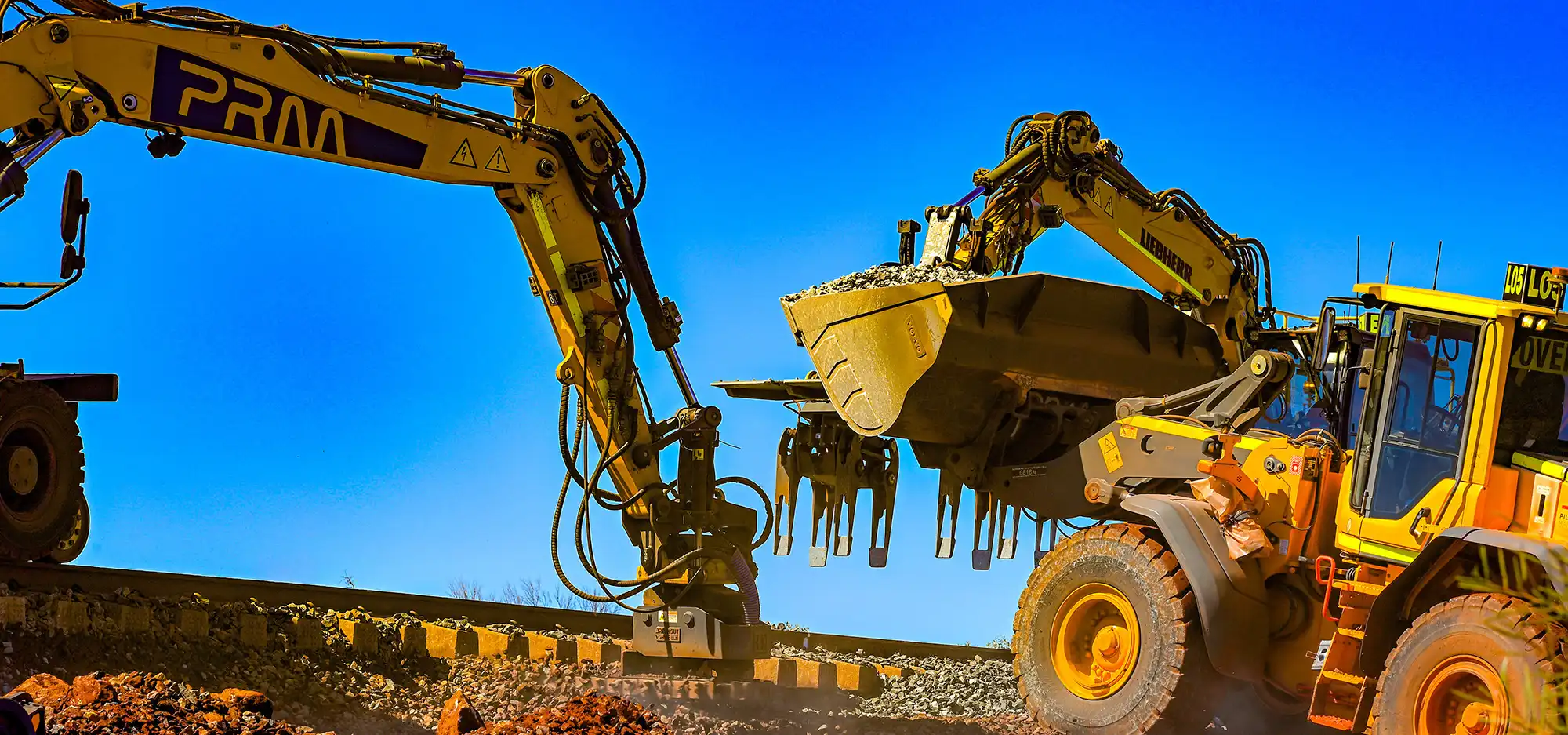